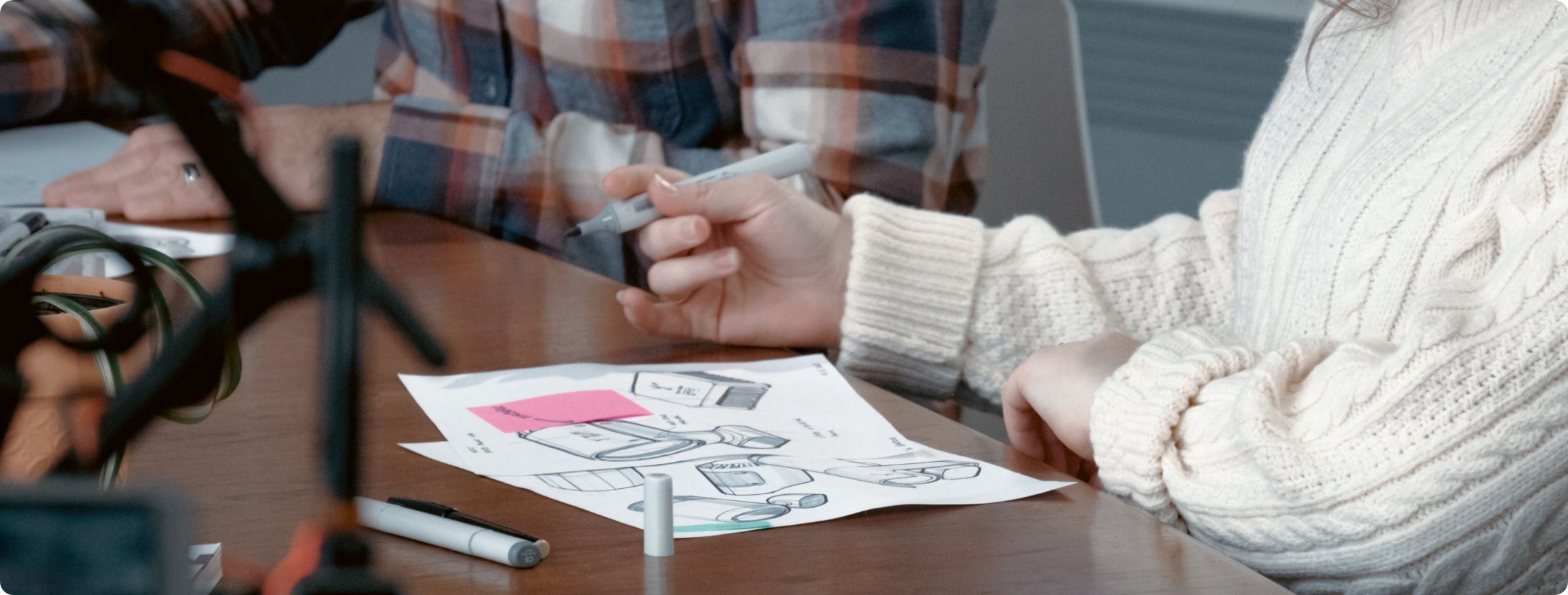
Designing for Impact. Developing for the Future.
Here’s your go to guide for sustainable product development > download here.
At Kaleidoscope Innovation, we help companies create smarter, more sustainable products through a proven, intentional approach to Design for Environment (DfE). Whether you're building something new or rethinking an existing product, our process helps reduce environmental impact across the entire product lifecycle.
Step 1: Identify Environmental Impact Hotspots
We begin by identifying which stages of your product’s lifecycle carry the greatest environmental burden. This helps prioritize design decisions that yield the most sustainable outcomes.
Consider the full product lifecycle:
- Raw Material Extraction – What’s required to source and process your materials?
- Production – How energy-intensive is manufacturing?
- Distribution – What’s the transportation footprint?
- Use Phase – Does your product consume energy or resources during use?
- End-of-Life – What happens when the product is no longer needed? Landfill, recycling, or reuse?
Key metrics: CO₂e emissions, energy use, resource depletion, water usage, waste, and pollution.
Step 2: Sustainability-Focused Brainstorming
With impact areas identified, we guide teams through targeted ideation. Example prompts include:
- How might we reduce plastic usage?
- How might we design this for disassembly and recycling?
- How might we extend the product’s usable life?
- How might we minimize energy consumption in use?
These focused prompts keep environmental responsibility front and center during early concept exploration.
Step 3: Concept Development with Sustainability in Mind
We embed sustainability criteria into concept selection and evaluation—both qualitatively and quantitatively.
Best practices include:
- Clearly identifying and communicating sustainability benefits in each concept.
- Including lifecycle impact assessments in selection criteria.
Step 4: Sustainable Design & Engineering
Our designers and engineers apply DfE principles to reduce environmental impact without sacrificing performance.
We consider the following nine sustainable design strategies:
- Longevity – Design for durability and long-term performance.
- Materiality – Use recycled, recyclable*, compostable, or low-energy materials.
- Dematerialization – Minimize the amount of material used.
- Repairability – Use accessible fasteners, avoid adhesives.
- Modularity – Design swappable components to extend product life.
- Component Reduction – Fewer parts = less waste and simpler assembly.
- Energy Efficiency – Optimize for low power use and renewable energy compatibility.
- Disassembly – Ensure components can be separated for recycling*.
- Remanufacturing – Enable re-use of containers or product components.
*Keep in mind: most users won’t recycle unless it’s easy and intuitive.
Step 5: Testing & Iteration
We simulate real-world conditions, including worst-case scenarios, using lean, repeatable methods. We aim to reduce material waste by reusing test samples and limiting sample size with engineering rationale.
Let’s Build Smarter, Cleaner Products
Kaleidoscope is your partner in eco-conscious product development. From concept to commercialization, we combine innovation with sustainability to future-proof your product and brand.
Ready to design with the planet in mind? Let’s talk about your project.
Back to Insights + News