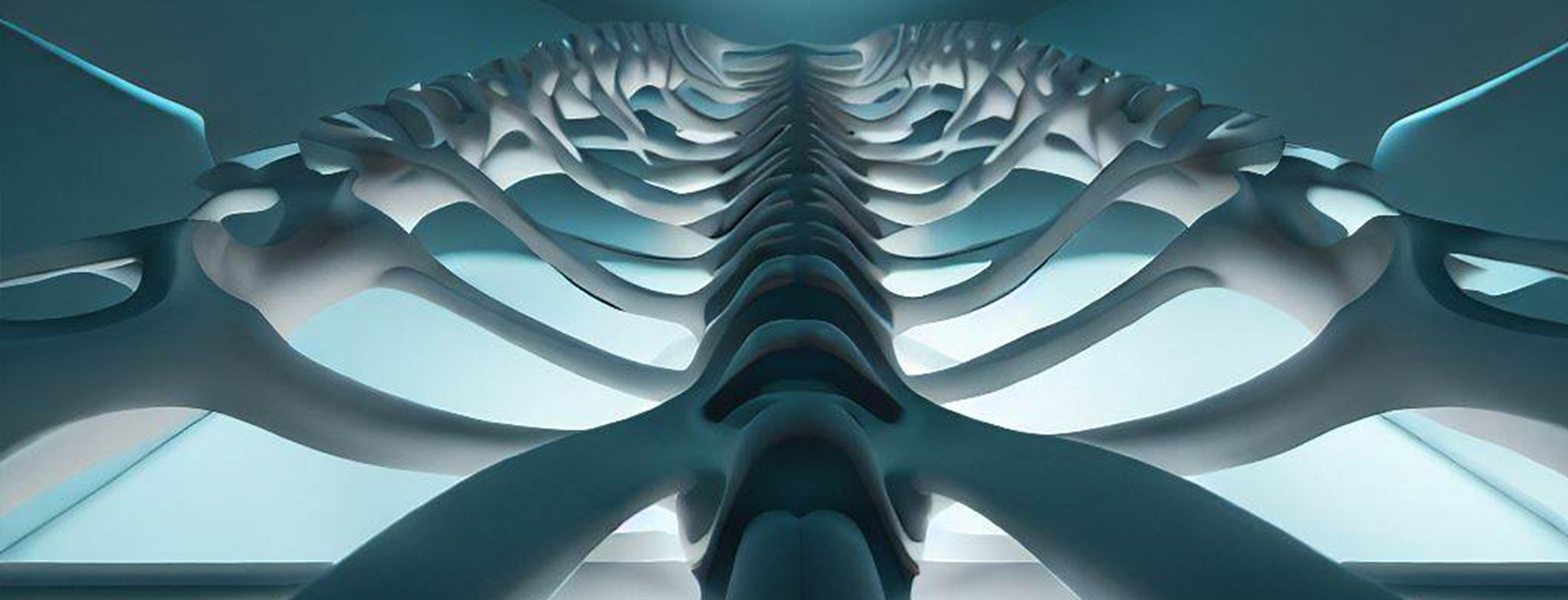
In the orthopedic industry, ensuring patient safety, minimizing infection risks, and optimizing cost-effectiveness are paramount considerations. To achieve these goals, three key elements play a crucial role: sterilization, reusable instrumentation, and packaging. In this article, we explore the best practices of this triad from an expert's perspective, emphasizing the impact on patient outcomes, operational efficiency, and environmental sustainability within orthopedic product development.
Sterilization: A Critical Imperative in Orthopedic Product Development
Sterilization is a fundamental aspect of medical device product development, manufacturing, and usage. By eliminating microorganisms and reducing the risk of surgical site infections (SSIs), proper design and sterilization protocols safeguard patient safety. The chosen sterilization method, such as steam, ethylene oxide, or gamma irradiation, will impact both material choice and part geometry.
Many plastics are not temperature stable with steam and may degrade with gamma irradiation. Tight interfaces and blind holes challenge EO gas / steam penetration to all host sites. And depending on how packaging is configured on a sterilization pallet, large devices may shield others from receiving a full dose of gamma ray. The rigorous validation of both cleaning and sterilization processes adhering to regulatory standards are essential to maintain the orthopedic instrumentation and implants.
Packaging: Safeguarding Integrity and Sustainability
Whether it’s a single use peel pouch or reusable surgical case, orthopedic devices require specialized packaging to ensure product integrity, sterility maintenance, and efficient handling.
Peel Pouch/Tray: Engineering seal width both for sterile integrity and ease of use. Heavier devices are more likely to put stress on sterile seal unless properly constrained. Right-size pouches within cartons to minimize creases, opt for a gentle roll instead. Execute verification tests after accelerated, real-time aging, and ASTM D4169 transit simulation. Testing doesn’t end at submission, incorporate in-process testing per ASTM F88 for ongoing vigilance.
Reusable Surgical Case: Layout instrumentation/implants as it makes sense for the procedure work-flow with spacing that allows steam ingress. Orientation angle should facilitate shedding of moisture, avoid any upward facing cavities as to prevent condensation pooling. A large amount plastic instruments in the tray puts you at risk of failing dry time testing. Keep total tray weight within bounds of regional requirements.
In addition, incorporating usability testing on packaging designs will help facilitate proper aseptic presentation and a smooth transition from sterile to non-sterile environments are essential for healthcare professionals. Optimal packaging design also considers sustainability aspects, such as the use of eco-friendly materials and minimizing excess packaging waste.
Regulatory Compliance, Quality Assurance, and Continuous Improvement
Sterilization, reusable instrumentation, and packaging are tightly regulated areas within the orthopedic industry. Regulatory bodies, such as the FDA and international standards organizations, provide guidelines and requirements to ensure the safety and efficacy of devices. Compliance with these regulations is essential to gain market approval and maintain patient trust. Manufacturers must establish robust quality management systems, conduct thorough validation studies, and implement effective quality control measures such as inspection and quarterly audits to ensure the reliability and consistency of sterilization, reusable instrumentation, and packaging processes. See ISO 11737, 11137, and AMI ST79.
Thanks to orthopedic research, device designs are continually advancing highlighting new materials and features. This progress extends to quality improvement projects, sterilization methods, and packaging innovations. Collaboration between industry expert consultants and regulatory authorities is vital for driving innovation and ensuring that decision making considers whether changes can be adopted into previous studies or if new testing is required.
Sterilization, reusable instrumentation, and packaging form a critical triad in the medical device industry, encompassing patient safety, operational efficiency, and environmental sustainability. Through meticulous sterilization protocols, the use of reusable instruments, and the development of optimized packaging solutions, orthopedic professionals can enhance patient outcomes, reduce costs, and minimize their ecological footprint. By prioritizing regulatory compliance, fostering continuous improvement, and embracing innovative technologies, the orthopedic community can maintain the highest standards of quality and safety. It is only through a comprehensive understanding and integration of sterilization, reusable instrumentation, and packaging practices that orthopedic product development teams can continue to evolve and flourish while delivering exceptional care to patients.
Back to Insights + News