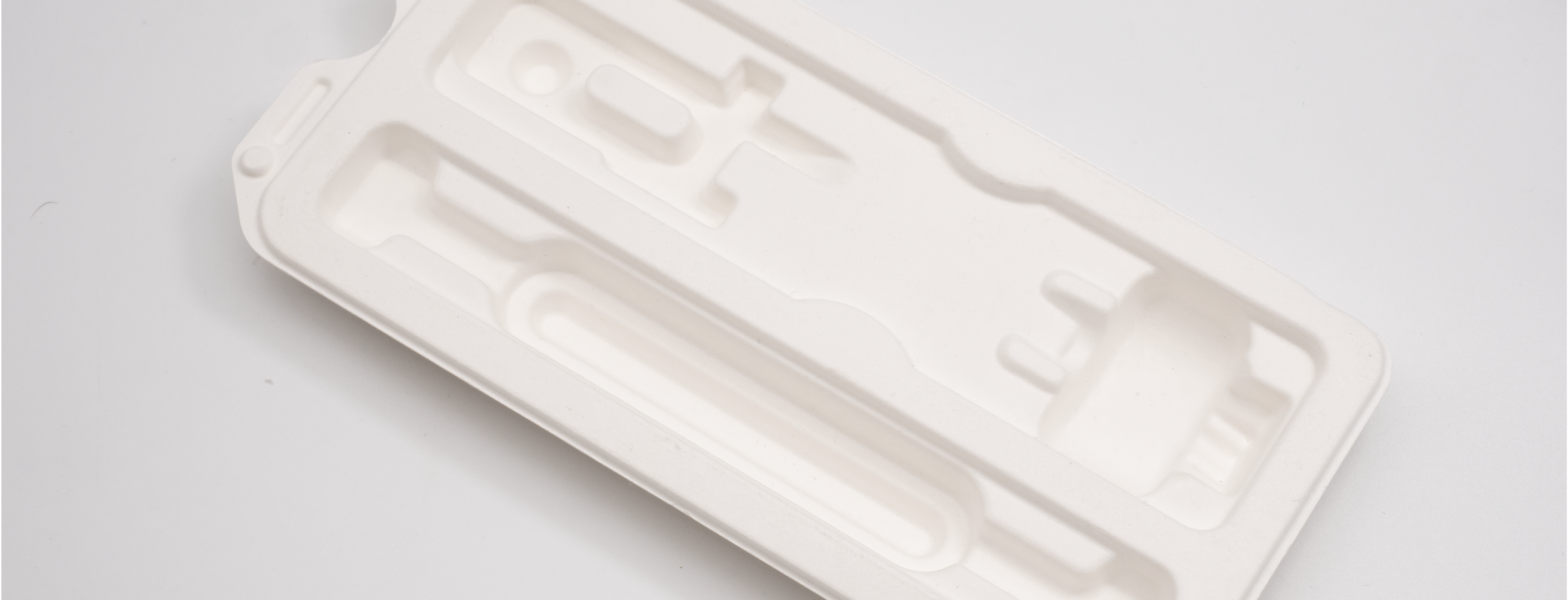
Over the past year, Kaleidoscope has begun to identify areas of opportunity for sustainability improvements within our culture and the products we design. One area we have been exploring is the potential of alternative materials within our product development process. Through a vendor partnership with 3D Color and RyPax, the team has been able to perform a preliminary evaluation of a molded fiber tray through small batch prototyping.
What is Molded Fiber?
Molded fiber or molded pulp is a material used for making molded forms from a variety of natural fibrous materials and/or recycled paper pulp. It is commonly used for a variety of packaging applications, from clamshell containers to consumer electronics packaging. The Kaleidoscope team was eager to evaluate potential packaging and product designs utilizing this technology. To do so, we teamed up with 3D Color to produce a small batch of 100 trays, which were originally designed for thermoformed plastic sheet.
Process and Environmental Impact Considerations
The mixed material used to make these trays contained bamboo fibers and bagasse, a by-product of sugarcane processing. There are a variety of other types of natural materials that can make up the base mixture, resulting in different physical properties.
The team also learned that there are two different methods that can be used in the molding process: dry press and wet press. The trays that were evaluated were generated via the dry-press method, where the material is formed in a tool, dried, and cured. These trays have a 1.2mm wall thickness and ~5° draft angle. The maximum wall thickness that can be achieved with this method is ~2.0mm. The minimum draft angle that can be achieved is ~5°.
The wet-press, or “heated-press” method, differs in that the mold is formed using a heated tool. With this method, the maximum wall thickness is ~1.2mm and minimum draft angle of 1° draft can be achieved. Wet press can produce a higher fidelity finish, though the heated tool requires more energy than the dry press method.
Preliminary Performance Evaluation
Upon receiving the batch of dry-press trays, some qualitative observations were able to be made:
- Features and edges were surprisingly sharp and visually on par with what’s expected from plastic thermoforming.
- Structural strength was similar to an egg carton, even with a significantly thinner wall thickness.
- A uniform off-white color was achieved. Fibers that make up the tray were visible upon close inspection.
- The material released particulate when stressed, with the particulate being very small pieces of the fiber.
- The underside of the trays had a slightly rougher surface due to the screen used in the molding process for moisture evacuation.
To understand the trays’ performance over time, we also performed simulated accelerated aging. We stored the trays at 60degC for 30 days, which is approximately equal to one year of aging, per the Arrhenius equation. The team noted several observations after removing the trays from the aging chamber:
- Slight warping was present in some samples.
- Accompanying creases seemed to occur in areas that were not stiffened by curved/bent geometry.
Design Considerations
This exercise just scratched the surface of testing needed to ensure a product made using this technology meets its requirements. However, it allowed for several basic discoveries that will inform how we might use this manufacturing process in the future. Moving forward the team has determined that the following should be considered, depending on the application and the requirements:
- Material
- What different natural fiber material sources yield significantly different properties? (e.g., Do corn husks have the same properties as bagasse?)
- Thickness
- What is the right thickness for the application?
- Simulated Environmental/Distribution Testing
- Whether the recycled paper pulp and/or natural fiber-based material is the product or the packaging, does it survive expected conditions? Shipping, temperature and humidity fluctuations, and shelf life are all variables that need to be considered.
- For sealed packaging, how well does the material keep water out? How well does it “breathe”?
- Coatings, including thin sheet PLA.
- How well does coating remain applied to tray?
- What properties does the coating give to the tray? Water resistance, decreased particulate shedding?
- Printing/Marking/Adhesives
- Can the material receive printing/stamping?
- Can dyes be added to the material?
- Do stickers or adhesive remain adhered?
- Cost
- What is the order quantity and required fidelity?
- In general, it was learned from the experience of our partners that the cost of molded fiber parts is approximately 2-3 times that of a plastic vacuum formed part in a production run. What does this mean for trays that are more complex?
- Sustainability
- Are the perceived benefits of using the molded fiber material overcome by the accumulation of energy, coatings, markings, etc. that may be used in making this product?
These tray prototypes were high fidelity and can prevent the need for expensive and time-consuming production-quality tooling early in the development process. Fibrous particulate is present on and in this material. If your product is sensitive to foreign material, a coated molded fiber tray is likely a better choice than an uncoated tray. Heat/aging seems to influence the integrity of the part, though this is only a preliminary finding. Due to relatively low structural strength compared to plastic, we recommend designing for strength, and reducing stress concentrations where possible. We are still evaluating this technology, and fortunately, partners like 3D Color make the iterative design and test cycle faster and less costly.
What’s Next?
Leveraging diverse design and manufacturing experience, evaluating new technologies and materials, and cultivating strong vendor relationships is nothing new for Kaleidoscope. Though these are among our strongest skillsets, we recognize that there is significant potential to better drive sustainability within the products we design and provide meaningful material and technology alternatives for the clients we serve.
About the Authors/Companies:
Kaleidoscope Innovation
- Headquartered in Cincinnati, Ohio, Kaleidoscope Innovationprovides medical, consumer, and industrial clients with full-service insights, design, human factors, and product development. For more than 30 years we have been helping our clients grow their capabilities, gain usable knowledge, and get worthwhile results. As a full-spectrum product design and development firm, we are an expert extension of your product vision. Our teams collaborate across disciplines, providing specialized input to produce the ideal intersection between function and form. To ensure the soundness of our work, Kaleidoscope houses a full range of test labs, and we employ an award-winning team that embraces every challenge, applying their experience, ingenuity, and passion.
3D Color:
- We help our clients shape first impressions into lasting ones. At 3D Color, we help the world’s best designers, marketers, brand builders and researchers bring their ideas to life. With industry-leading capabilities in advanced prototyping, exceptional comp production, custom color development, efficient sales sample programs and an innovation incubator, we’re a full-service strategic partner to the visionaries who are shaping the future of packaged goods.
Grant Cothrel
- Sr Design Engineer
- Grant enjoys being faced with new challenges and recognizes that well-designed products lead to better experiences and outcomes for users. He loves the design process and has operated primarily in medical device and industrial instrumentation. His passion to understand, innovate, and simplify has been supported and strengthened by the Kaleidoscope team and their talented partners. At home, he always has a fun project in the works (think: wooden bicycle, handheld Theremin, one-string electric guitar)!
Sophie Fain
- Industrial Designer
- As a part of the Kaleidoscope team, Sophie has had the opportunity to collaborate with diverse and talented individuals to understand complex problems and provide meaningful human-centered solutions. Sophie is driven by the chance to create a positive emotional connection with users through the experiences she crafts. Prior to joining Kaleidoscope, she has worked for companies like Depuy Synthes of Johnson and Johnson, The Clorox Company, and a physical therapy startup, BAND Connect. When she is not captivated by a design problem, Sophie enjoys getting her creative energy out through activities like pottery and cooking.
Mike Corbett
- Director of Model Services
- Mike leads the model shop team at 3D Color and utilizes a wide range of techniques to meet clients’ challenges. With 28 years of experience and a passion for model making, Mike leads by example and teaches his craft to his team and to the company’s clients. Mike enjoys the “hands-on” nature of our work and the problem-solving thinking needed to complete projects. In his free time, Mike enjoys his family, travel, and the wicked game of golf.