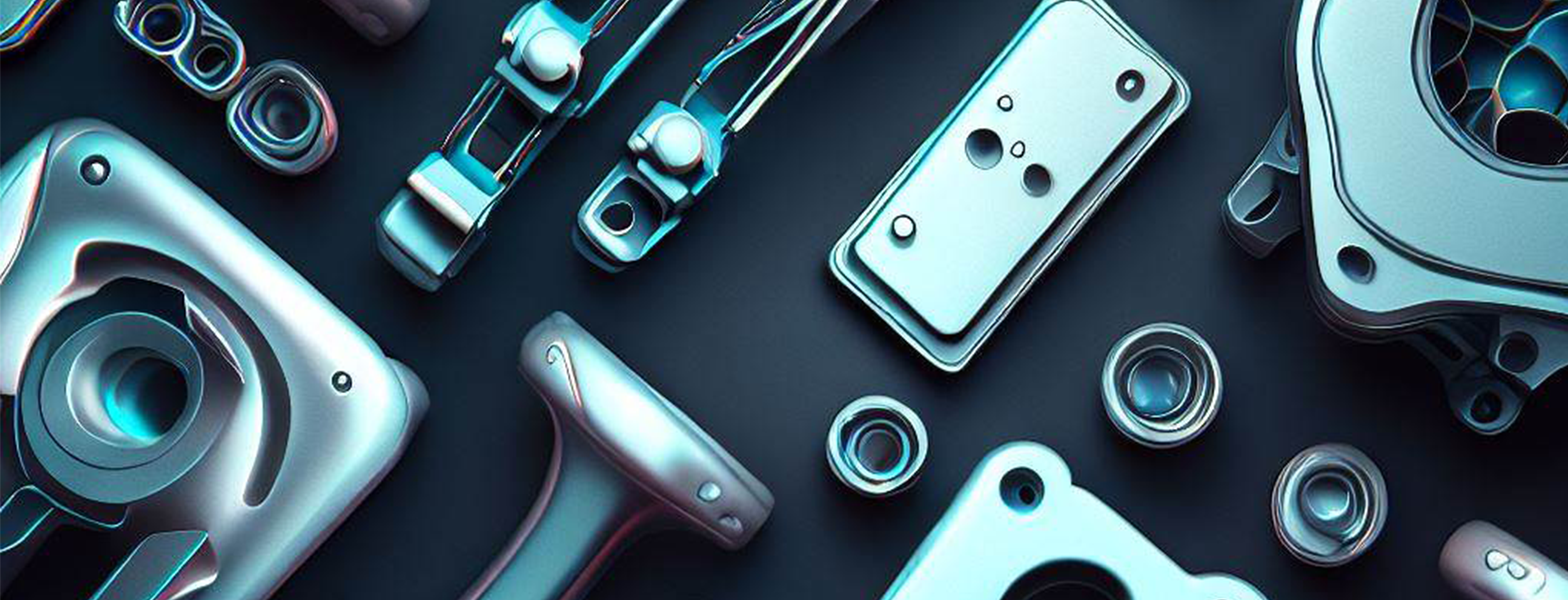
Rapid prototyping has emerged as a transformative force within the field of orthopedic device development, reshaping the way medical devices are conceptualized, tested, and brought to market. In this article, we delve into the substantial influence that rapid prototyping is exerting on the orthopedic industry, exploring its advantages, applications, and prospective implications.
Accelerating Innovation and Iteration through Orthopedic Product Development
The dynamic realm of orthopedic product development has found a robust ally in rapid prototyping. This innovation leverages advanced 3D printing and additive manufacturing technologies to swiftly transform digital models into tangible prototypes. In a mere matter of hours or days, engineers and designers working on orthopedic research can iterate and refine designs, hastening the innovation cycle. This acceleration paves the way for speedier iterations, efficient incorporation of feedback, and optimal design enhancements. The outcome? Augmented device performance, elevated functionality, and an expedited journey from concept to commercialization.
Customization and Personalization in Orthopedic Device Design
Orthopedic devices necessitate tailored solutions to harmonize with the distinctive anatomical requisites of individual patients. The prowess of rapid prototyping empowers product development teams to craft patient-specific orthopedic implants and instruments. This is achieved through the fusion of advanced imaging techniques, computer-aided design, and orthopedic design consulting. By capitalizing on these rapid prototyping technologies, orthopedic professionals can engineer bespoke solutions that not only offer impeccable fit, but also precise alignment and superior functionality. The upshot? Optimized patient outcomes, heightened satisfaction, and an orthopedic product development landscape poised for transformation.
Efficient Testing and Validation of Orthopedic Devices
Prototypes conjured through rapid prototyping techniques transcend the realm of theory. They are subjected to rigorous testing and validation processes that mirror real-world circumstances. For orthopedic product design teams, this means a proactive identification of potential design glitches, a comprehensive evaluation of performance parameters, and steadfast regulatory compliance. By fostering an environment of early feedback and iterative testing, manufacturers can effectively curtail errors, slash costs, and expedite the time to market for orthopedic devices. The outcome? Enhanced efficiency, reduced risk, and orthopedic product development that adheres to the highest standards.
Collaboration and Stakeholder Engagement in Orthopedic Design Consulting
The power of rapid prototyping extends beyond the realm of design teams to foster productive collaboration among diverse stakeholders in orthopedic device development. By providing tangible prototypes for visualization and interaction, rapid prototyping emboldens surgeons, engineers, and stakeholders to contribute valuable insights. This collaborative approach facilitates informed decisions regarding design adaptations, usability enhancements, and functional requisites. The ultimate goal? Orthopedic instrumentation that seamlessly align with the desires and needs of end-users, culminating in heightened adoption and acceptance within the healthcare community.
Cost-Effectiveness, Risk Mitigation, and Orthopedic Engineering
The conventional pathways of orthopedic product development are often fraught with steep upfront costs, protracted timelines, and inherent risks. Rapid prototyping emerges as a potent antidote to these challenges, seamlessly curtailing development costs and compressing timeframes. Moreover, it serves as a vanguard against design pitfalls, identifying and resolving issues in their embryonic stages. By harnessing the potential of rapid prototyping, orthopedic product development teams adeptly allocate resources, attenuate financial risk, and usher innovative products to market with unprecedented efficacy.
Future Implications of Orthopedic Device Engineering
The impact of rapid prototyping in orthopedic device development is poised to burgeon exponentially in the forthcoming years. As materials, 3D printing technologies, and artificial intelligence continue to evolve, innovation will flourish, enabling the genesis of intricate and sophisticated orthopedic devices. Rapid prototyping shall remain at the heart of translating these breakthroughs into tangible solutions, relentlessly pushing the boundaries of orthopedic care.
In conclusion, the landscape of orthopedic device development stands forever transformed by the advent of rapid prototyping. Through its application, orthopedic professionals have been empowered to create patient-specific solutions, improve device performance, and enhance patient outcomes. With the orthopedic industry embracing rapid prototyping technologies, we can expect an accelerated pace of innovation, a more personalized approach to care, and the development of advanced orthopedic devices that will shape the future of musculoskeletal medicine.
Back to Insights + News